Why Are We Strict About Print Job Cut Off Times?
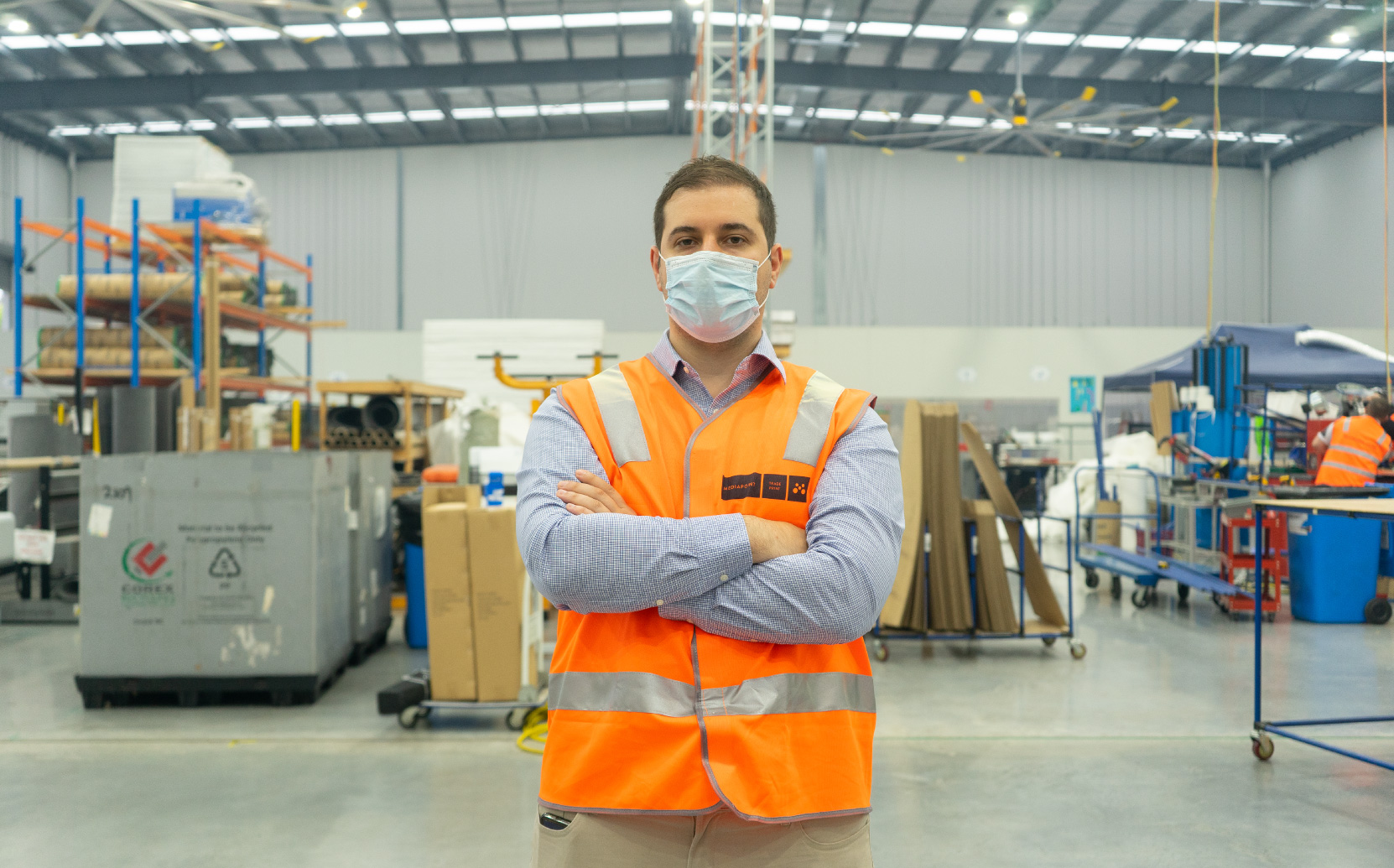
Read on (and watch) to learn why we have strict, print job cut off times for certain products. We break down how that enables service levels above and beyond the competition.
Mediapoint averages 150+ orders a day. To deliver on these with next-day turnaround, we have established Lean processes that other trade printers can’t compete with.
A strict printing cut-off time of 12pm underpins these procedures. At this time, every day, our system automatically locks out any new next-day orders. From there, automations begin to run; preparing all inventory, equipment, artwork files and staff required for a batched print run.
Print Job Cut Off Times Create Predictability
Keeping strict printing cut off times (and making it clear to customers) means a predictable service level for customers. With no variance in lead times they have peace-of-mind that jobs will be completed and dispatched as expected.
It means that our printing teams have a clear set of tasks to complete. That means we can adequately prepare our lines for maximum efficiency. Set print job cut off times are key to batching jobs, minimising change to stock and print modes during operation.
We’ve previously discussed locking into one print mode only which helps maintain quality and speed.
Printing Once A Day Reduces Costs
We pride ourselves on offering the best prices. To do so we need to find savings wherever possible – all of which are passed onto our clients. Inventory represents a significant portion of any print cost. A batching process helps us keep an optimal amount of inventory on hand. Plus, we end up using less resources per print run. Trade printers need definitive print job cut off times to effectively schedule completion of these job batches.
Another overlooked cost of printing is labour. This rises significantly when print runs are not batched. The time it takes to set up equipment for each differing print run, to cut print jobs, to complete finishing work and to package items are all areas where great savings can be made. In combination with our automated PrintIQ system – which reduces the need for manual servicing of quotes and design – we significantly reduce costs.
These savings then provide margin for our print reseller customers to play with when on-selling work.
Mediapoint’s Print Process Benefits Our People
The batching process and printing cut off times mentioned above mean our staff just need to complete each task once before moving onto the next stage of the print run. They become more efficient and we can do more, with less people. Unlike other trade printers, our teams are not burdened by wastes of rework or overproduction. In fact, our staff gain valuable time back and are involved in every stage of the work, allowing them to build and maintain their skillset.
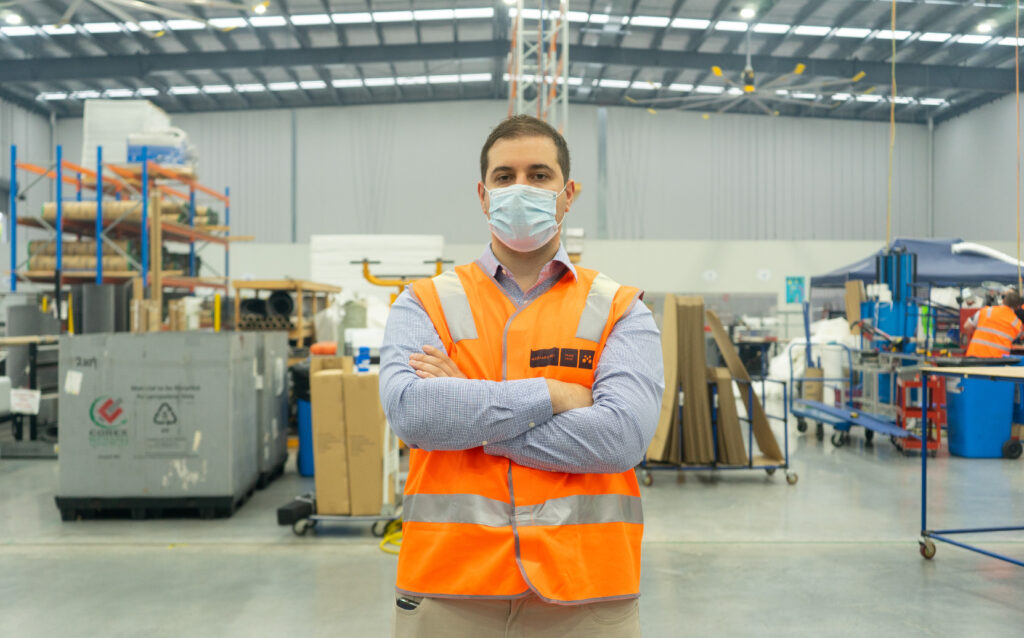
Our Process Keeps Us Honest
Our established, automated system for overnight printing means there is minimal variance in our output and a predictable low-touch level of service. This reduces friction in the ordering process, and allows us to be transparent about how jobs are handled.
This visibility is useful for resellers looking for the right trade print partner for high volume output. It removes the guesswork involved in the print process for them and ensures they can deliver on service levels to their own customers.
We’ve established our print job cut off times based on experience and optimisation over the last 16 years of servicing high volume resellers. In that time we’ve identified that the 12pm cutoff provided an ideal lead-time for a majority of our clients and our internal processes. Furthermore when rush print jobs are required (which we don’t cater to) our customers’ in-house capabilities can handle them.
As we say, “the proof is in the print” so if you’re looking for a trade print partner that can deliver on high volume jobs day-in, day-out, give our 24-hour turnaround process a try on your next high volume print run. Simply sign up to PrintIQ here and order by 12pm for dispatch by next business day.